Our company has been approached by Volkswagen Slovakia, a.s. to deal with the use of machine learning and its implementation in defectoscopy methods. Defectoscopy is a non-destructive method that uses machine learning implemented by us to check the condition and quality of products in an industrial environment. Machine learning algorithms have a wide range of applications and their applications can be used in mathematical statistics or artificial intelligence and other areas of our daily life. In this project, minimizing the hardware requirements of the system implementation is an important factor.
Our challenge and objectives
Our challenge and goal were to use machine learning to increase the efficiency of defectoscopy by minimizing the need for manual inspection and reducing the number of errors and false positives. Machine learning can analyze large amounts of data and learn to recognize different patterns and anomalies in materials and products. These algorithms are able to detect defects and flaws that might be difficult for the human eye to see, increasing the level of accuracy and reliability of detection. Defectoscopy in materials and products is a critical process in many industries where even small errors can lead to serious problems and financial losses.
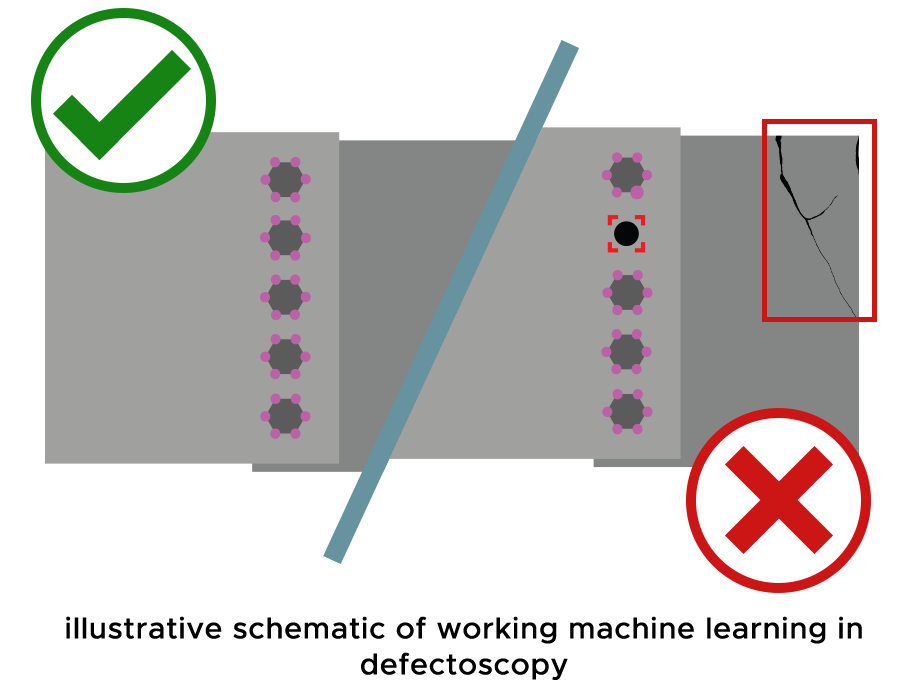
Our solution
he use of machine learning in defectoscopy can lead to improved manufacturing processes and reduced product defects, leading to greater customer satisfaction and increased profits for companies.Machine learning can also be applied in other areas such as medical diagnostics, security or cyber protection.
In the industrial environment, the use of artificial intelligence in defectoscopy has been key in recent times. Thanks to machine learning, it is possible to monitor and control the condition and quality of goods during production, in the automotive and engineering industries, defectoscopy is used to check joints, welds, rivets, screws of different parts, coatings, or anomalies that may have occurred.
Project complexity
Size
4/6

Financial complexity
4/6

Time complexity
4/6

Complexity
5/6

Customer benefit
The results of the project were successful for the client Volkswagen Slovakia, a.s. The solution itself was even presented at Volkswagen Innovation Days. The operation of such a solution is possible 24 hours a day, which guarantees continuous control and monitoring of production. The high accuracy of the system ensures that even small anomalies and deviations from the norm are captured. The elimination of human error ensures that products are controlled one hundred percent saving time and money is important for every business. Defectoscopy is suitable for checking and eliminating defects to an absolute minimum and saves time and money for any business.
